AC Floby is a leading manufacturer of brake components for passenger cars. In 2020, we delivered a quality inspection system, where the customer’s goal was to achieve a more qualitative and efficient production. The system consists of three inspection stations, each with a different purpose in the inspection process. It is based on a PC-based system where we combine 2D technology (area and linescan cameras) and 3D cameras. For image analysis, both traditional vision tools and AI are used. The cycle time in the cell is about 15 seconds.
At the first station, the system reads the part number of each brake disc that passes, as the products arrive at the inspection cell from two different production lines. This ensures that the correct product is inspected and that the required legal markings are in place.
In the second inspection station, the top and outer surfaces of the product are inspected. The system identifies defects such as casting pores, vibration damage, and machining damage with high precision. The system also ensures that no casting residues are stuck in the brake disc’s vents.
Using a robot that picks up and rotates the disc in the third inspection station, a complete inspection of the underside is enabled, where defects are identified in the same way as in the previous inspection station.
On two of the production lines, a fourth and complementary station for inspecting the painting was also added. Here, the system ensures that each disc is correctly painted, as some parts of the product should be painted, and others should not.
For AC Floby, the process has become both more reliable and cost-effective. In addition to a more consistent and reliable quality assessment, which reduces the number of customer complaints, an improved working environment is a significant gain. Previously, the inspection was performed manually during packing, and since the introduction of our system, along with automatic packing, work-related illnesses related to this process have disappeared.
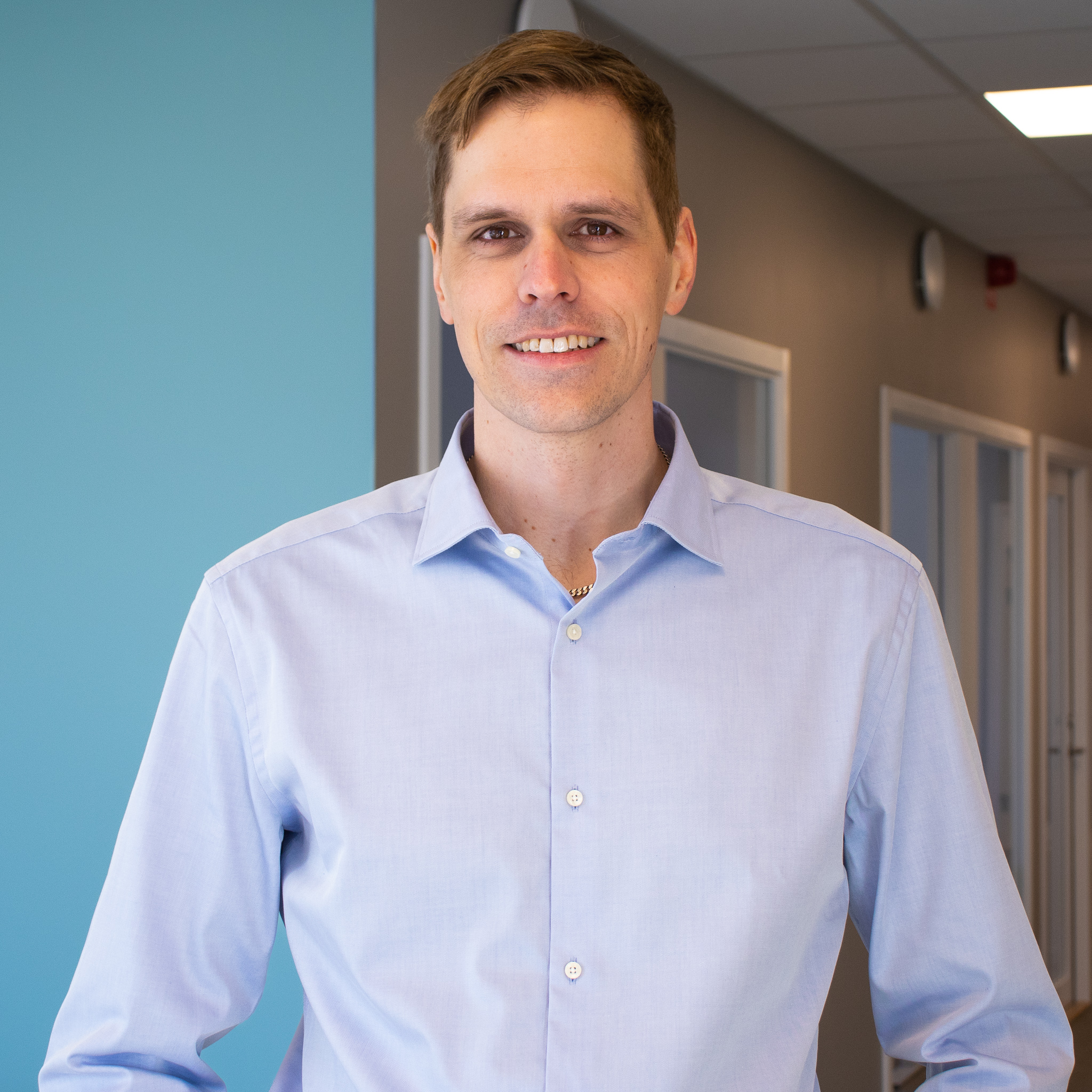
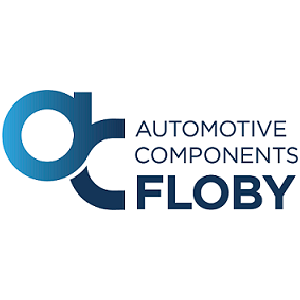