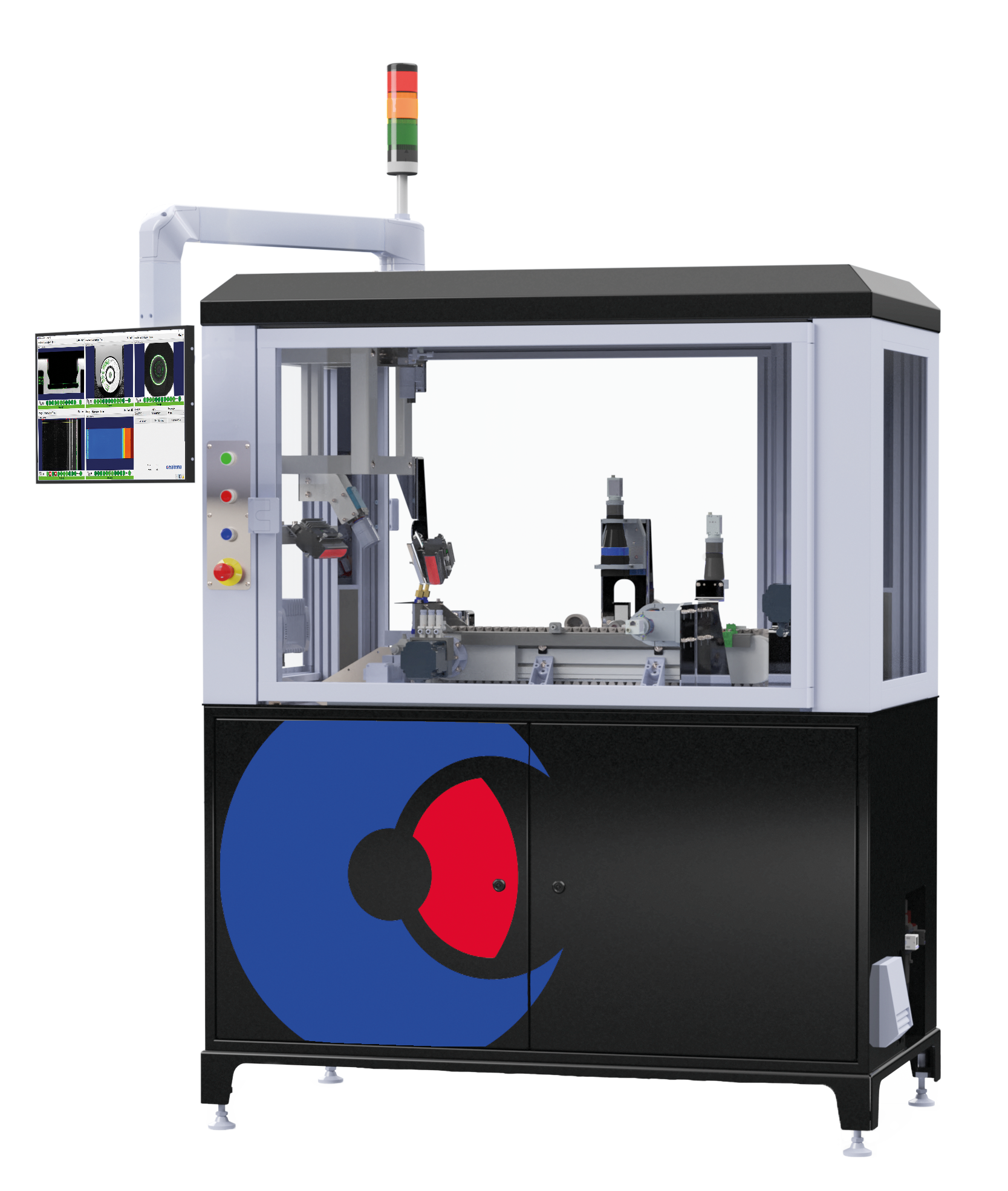
Elevate your production quality, efficiency and precision with InSpec.
Defect-based sorting
InSpec sorts parts by defect category – for instant, visual quality feedback.
Compact footprint
Among the smallest inspection machines on the market – minimal space, full capacity.
Quick caliber change
Change caliber in under three minutes – no camera or light adjustments needed.
Controlled feeding
Parts are servo-fed in fixed positions – ensuring stable flow and precise control.
Repeatability
Unmatched repeat-
ability. Reliable results – every time.
InSpec is carefully developed to objectively support and verify high quality ammunition production. Through single source laser triangulation, telecentric lenses and high resolution cameras, we can guarantee accurate inspection of bullets, cases and cartridges, free from multiple sources of miscalculations.
It objectively detects, identifies and quantifies critical defects. With the throughput of 120 parts per minute the machine can thoroughly detect 30+ defects, faster and more accurate than the human eye. Rejected parts are sorted into four different reject bins depending on the category of defect, enabling fast subjective inspection.
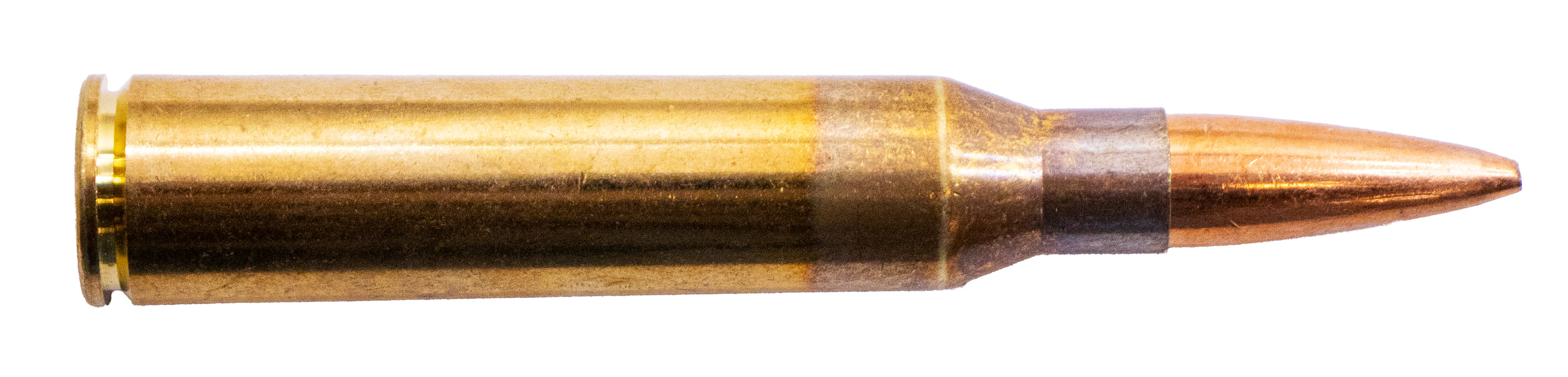
Head
1101. This image shows an example of a defect detail (chips in fire hole).
- Head stamp
- Primer presence, dents and scratches
- Colored sealant coating
- Crimp
- Flash hole presence, diameter and placement
- Chips or dirt in fire hole
Case
0405. This image shows an example of a defect detail (scratch).
- Bulges
- Cracks
- Dents
- Scratches
- Folds
- Total length
- Annealing
- Concentricity
- Surface stains
Projectile
0803. This image example shows a bullet with a colored tip.
- Bullet tip shape
- Wrong bullet type
- larger tip defects
- Color of paint
- Scratches
Extractor Groove
0109. This image shows an example of a defect detail (double extractor groove).
- Missing extractor groove/extractor defects
- Magnum belt
- Groove depth
- Extractor thickness and angle
- Rim thickness and diameter
- Extractor diameter
Mouth
0501. This image shows an example of a defect detail (chip in mouth).
- Missing material
- Cracks
- Circularity
- Chips
- Notches
- Burr
- Mouth folds
See how it works...
Additional features for more efficient handling
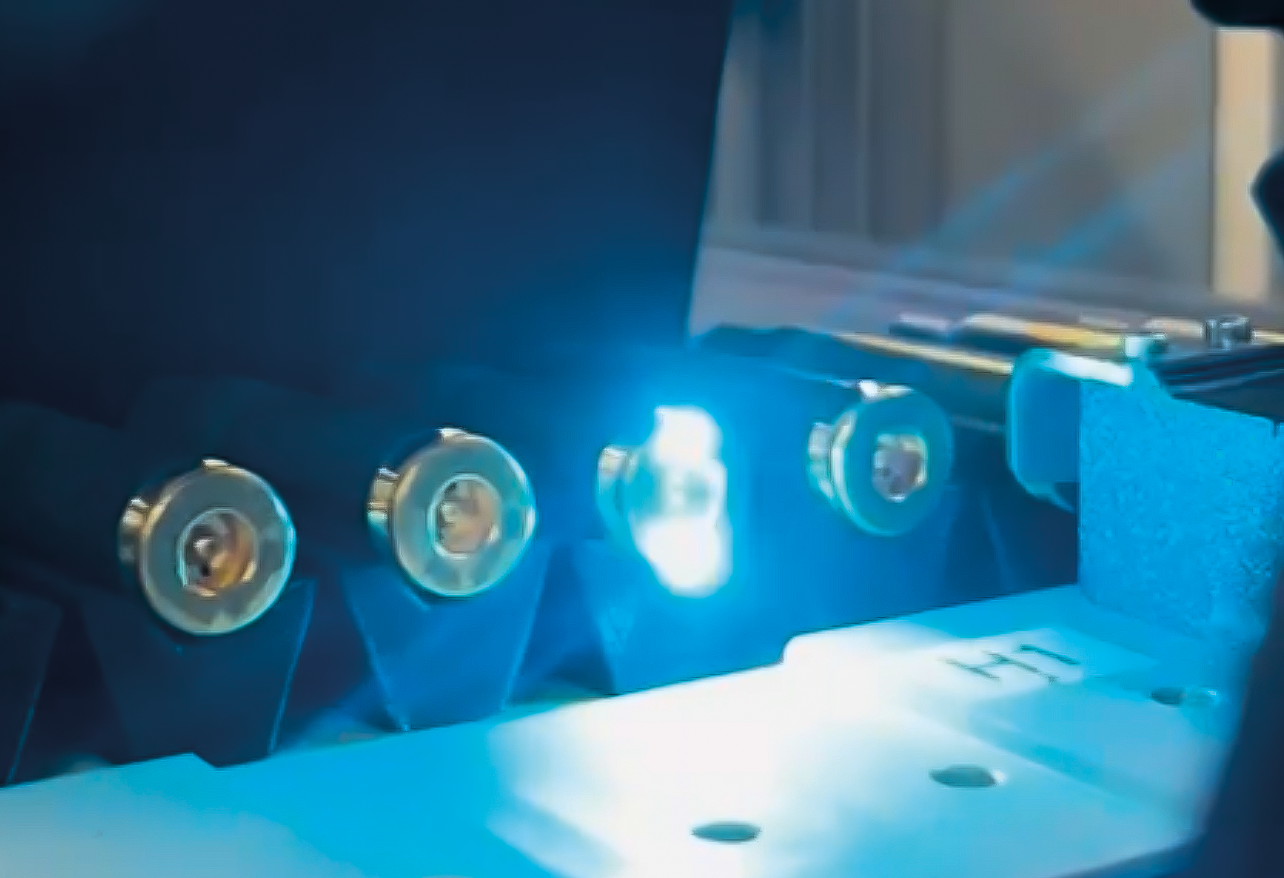
Laser marking of head stamps
To reduce your logistics costs our machines can be combined with integrated laser marking of your or your customers’ head stamps. Unlimited number of headstamps can be stored in the software library.
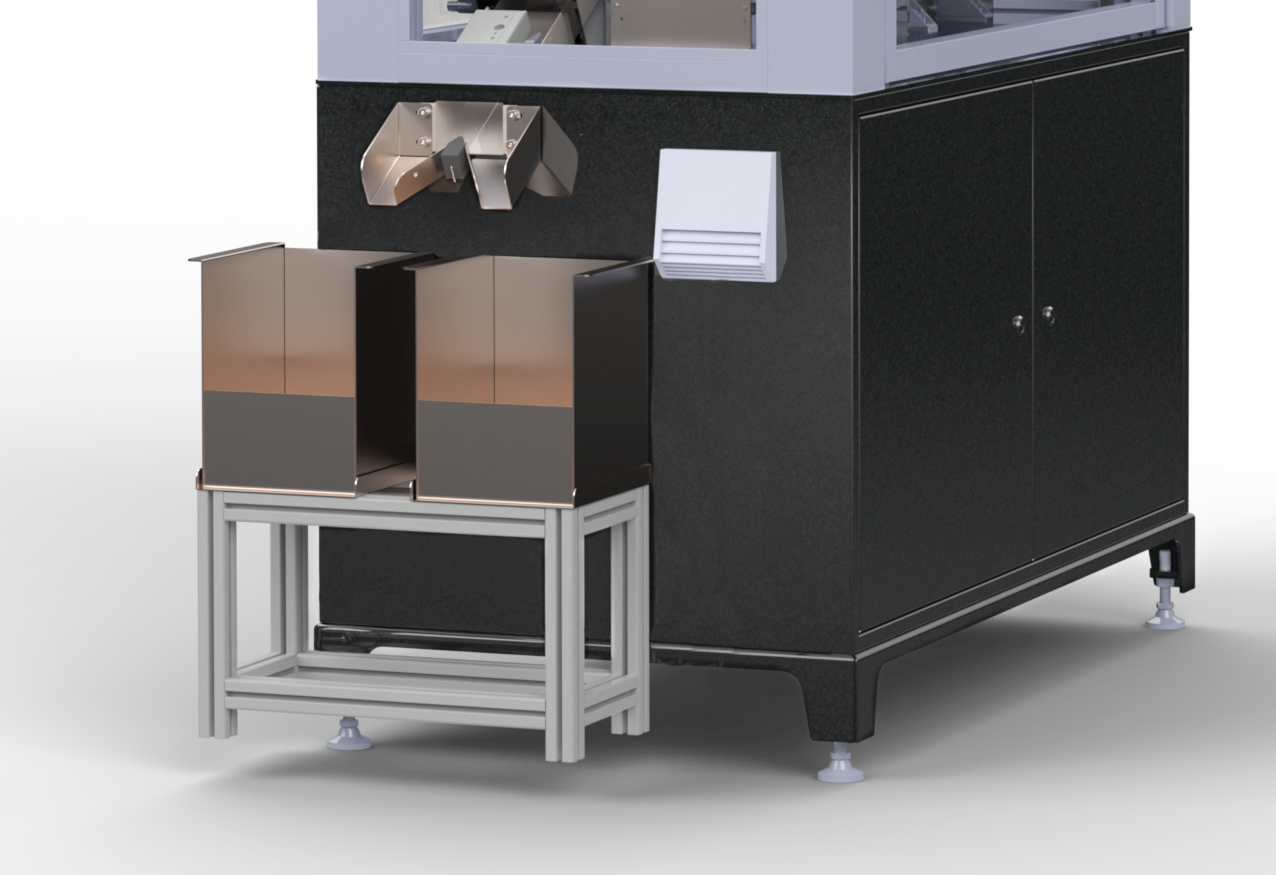
Automatic bag filler
For easy and accurate filling of ammo bags InSpec has an automatic bag filling function. When one bag is full, the machine automatically switches to the next. The number of parts in a full bag can be customized to your needs.
Customize InSpec for your needs
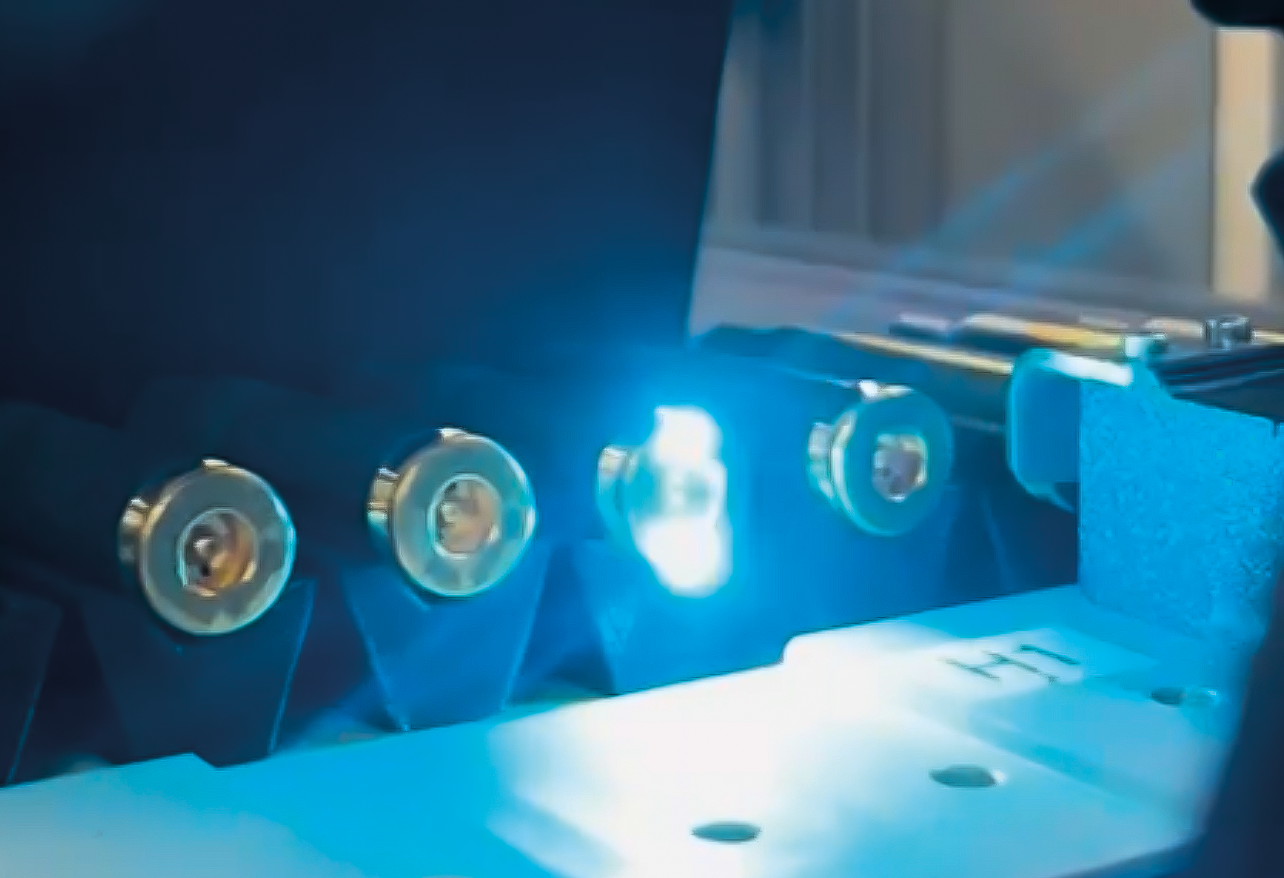
Laser marking of head stamps
To reduce your costs our machines can be combined with integrated laser marking of your or your customers’ head stamps. Unlimited number of headstamps can be stored in the software library.
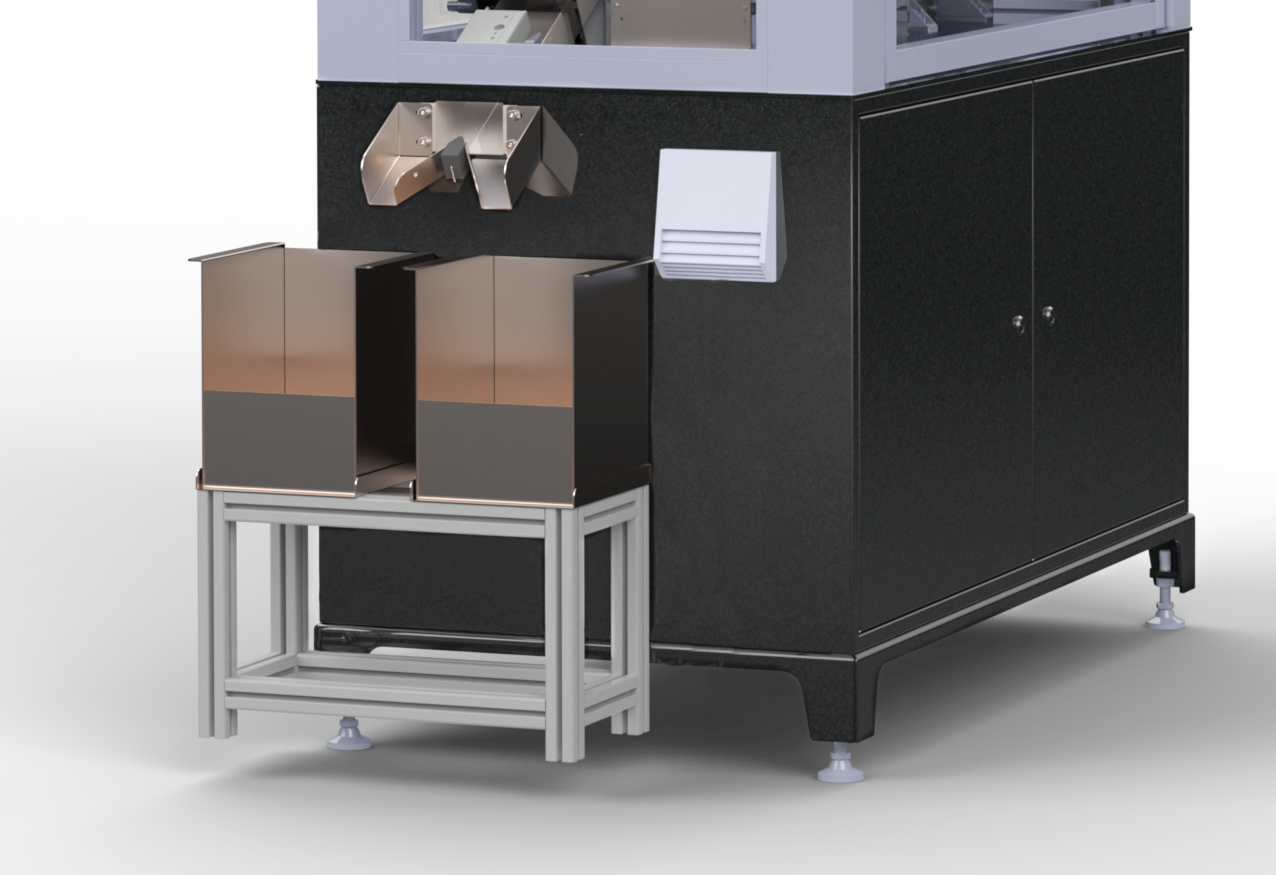
Automatic bag filler
For easy and accurate filling of ammo bags InSpec has an automatic bag filling function. When one bag is full, the machine automatically switches to the next. The number of parts in a full bag can be customized to your needs.
Joakim Schackenborg
Business Area Manager | Ammo
Do you want to learn more about InSpec and how it can meet your production quality needs?
Want to know more?
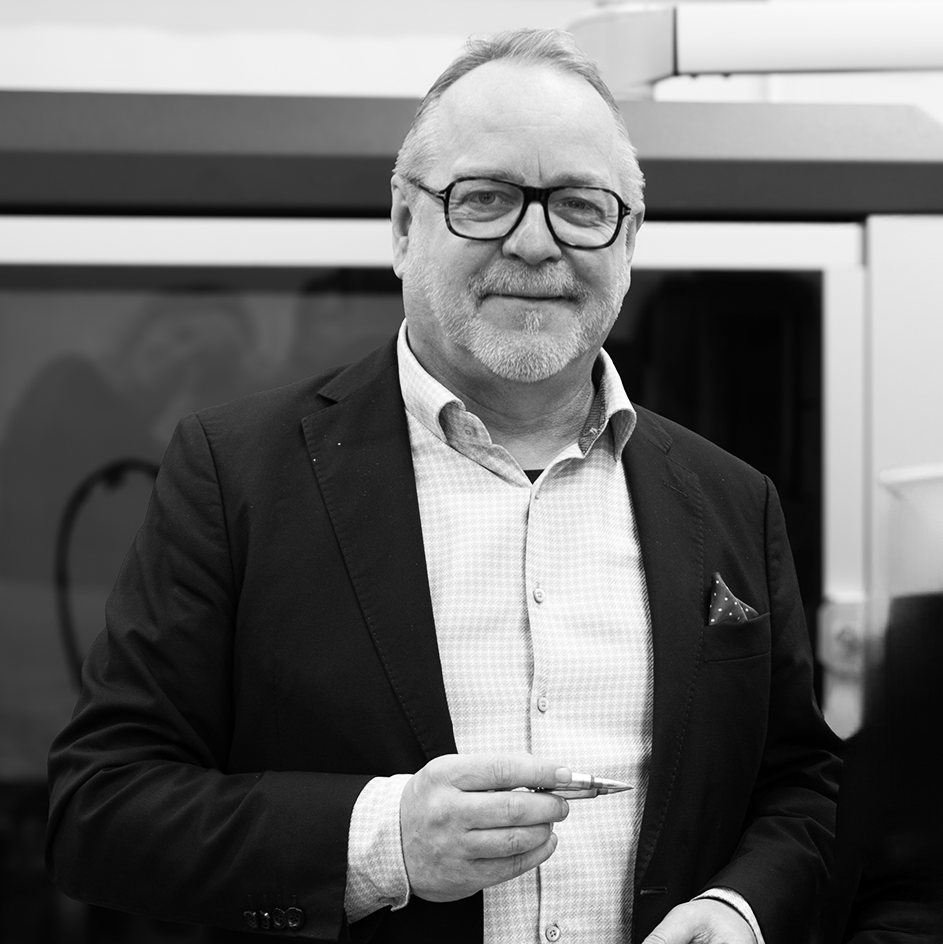
Joakim Schackenborg
Business Area Manager | Ammo